摘要:結(jié)合無錫金匱大橋鋼結(jié)構(gòu)(下承式鋼桁架+鋼箱梁結(jié)構(gòu)體系)工程的制造實(shí)踐,針對(duì)鋼桁架、鋼箱梁的結(jié)構(gòu)特點(diǎn)、加工制作的難點(diǎn)、重點(diǎn)以及實(shí)際施工條件,介紹了鋼桁架、鋼箱梁制造過程中的重點(diǎn)工藝技術(shù)及質(zhì)量保證措施。
關(guān)鍵詞:下承式體系 鋼桁架、鋼箱梁制造預(yù)拼裝 工藝技術(shù) 質(zhì)量控制
1 工程概況
無錫市太湖大道節(jié)點(diǎn)改造工程JKQ2 標(biāo)(以下簡(jiǎn)稱無錫金匱大橋鋼結(jié)構(gòu))采用了下承式鋼桁梁+鋼箱梁結(jié)構(gòu)體系,主橋跨徑布置為55m+105m+55m=215m,橋面為雙向八車道、兩側(cè)為非機(jī)動(dòng)車道和人行道。主桁由兩片鋼桁架組成,主桁中心距離33m,節(jié)間距離7~13.5m,主桁高度采用二次拋物線變化形式,兩邊跨矢高f=3m,中跨矢高f=10.5m,中支點(diǎn)處高17m。中間為鋼箱梁橋面,寬30m,在兩片主桁的外側(cè)各挑出5.9m的懸臂托架支撐非機(jī)動(dòng)車道及人行道,橋面總寬度46.0m。本橋整體結(jié)構(gòu)示意見圖1及立面布置見圖2所示。
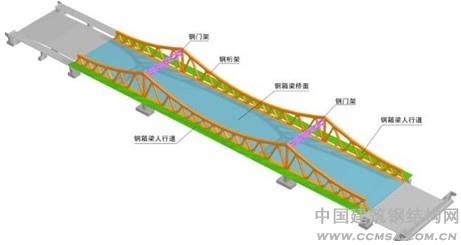
圖1 金匱橋鋼結(jié)構(gòu)整體軸測(cè)示意圖
圖2 金匱橋橋型立面布置圖
1.1 結(jié)構(gòu)形式
1.1.1 鋼桁架結(jié)構(gòu)形式
鋼桁架下弦和上弦系桿均采用了焊接整體節(jié)點(diǎn)結(jié)構(gòu)形式,鋼桁架上、下弦桿采用箱型截面,上弦桿件截面為□2215X1200X(20~28)X(20~32),下弦截面為□1500X1200X(20~36)X(20~32);鋼桁架斜桿和豎桿均采用焊接H形截面,截面尺寸為H1200X500X24X24、H1200X700X24X24、H1200X500X28X32、H1200X700X28X32、H1200X700X32X32、H1200X1100X32X40、H1200X760X32X32等,鋼桁架整體結(jié)構(gòu)示意圖見圖3所示。
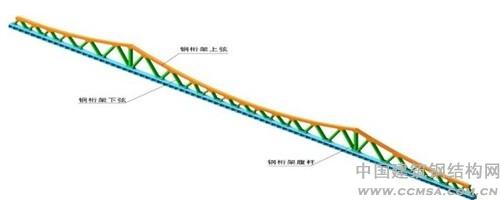
圖3鋼桁架軸測(cè)圖
1.1.2 橋面鋼箱梁結(jié)構(gòu)形式
橋面鋼箱梁總長(zhǎng)215m,寬度為30m,截面高度2.21~2.45m(頂板設(shè)有1.5%的斜坡),重約3580噸。主要由頂板(16m m)、底板(14m m)、縱向腹板(14m m)、橫隔板(14m m)、U形肋(8m m)、加勁板(10~14m m)等組合而成,橋面鋼箱梁整體結(jié)構(gòu)示意圖見圖4所示。
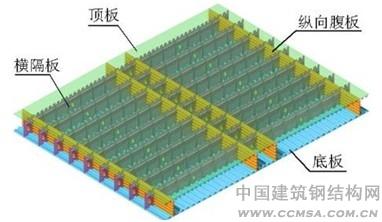
圖4 橋面鋼箱梁軸測(cè)圖
1.2 分段的劃分
1.2.1 鋼桁架分段的劃分
單榀鋼桁架上弦分為24個(gè)分段,其中A1A2~A11A12分別對(duì)稱制作各1件,中部分段為A12A13、A13A12’各制作1件。單榀鋼桁架下弦分為23個(gè)分段,其中E0E1~E10E11分別對(duì)稱制作各1件,中部分段為E11E11’制作1件,見圖5所示。
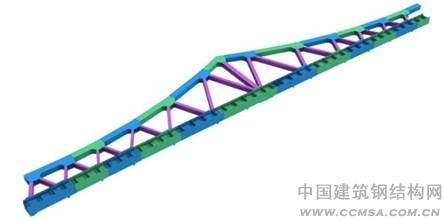
圖5鋼桁架分段劃分示意圖(以1/2為例)
1.2.2 橋面鋼箱梁分段的劃分
橋面鋼箱梁根據(jù)現(xiàn)場(chǎng)吊裝要求,將其劃分為23個(gè)節(jié)段,分別為節(jié)段A~節(jié)段L。其中節(jié)段A~節(jié)段K分別2件,節(jié)段L為1件,見圖6所示:
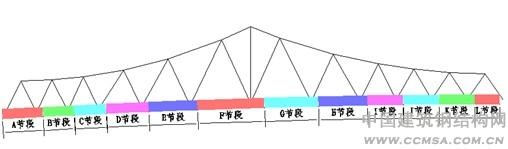
圖6橋面鋼箱梁分段劃分示意圖(以1/2為例)
1.3 連接節(jié)點(diǎn)形式
1.3.1 鋼桁架典型節(jié)點(diǎn)
鋼桁架上弦桿主要采用帶肋箱形截面桿件,弦桿與腹桿連接端采用了整體節(jié)點(diǎn)板構(gòu)造,并且腹桿與弦桿節(jié)點(diǎn)板間采用了插入式的栓接連接方法;弦桿與弦桿間的連接則是四周均采用了全栓接連接的形式,見圖7所示;
圖7 鋼桁架連接節(jié)點(diǎn)形式
1.3.2 橋面鋼箱梁分段間的連接
分段間頂、底板均采用焊接,頂、底板上U型肋、縱向腹板上加勁板通過制作嵌補(bǔ)段進(jìn)行連接,縱向腹板連接采用栓接,見圖8所示。
圖8 橋面鋼箱梁分段間連接示意
1.3.3 橋面箱形梁分段與鋼桁架箱梁間的連接
鋼桁架與橋面鋼箱梁間頂、底板均采用焊接,鋼箱梁橫隔板與鋼桁架上連接板采 用栓接,見圖9所示。
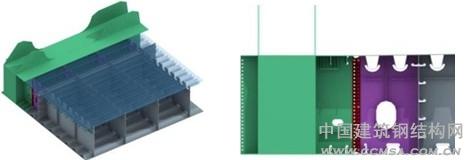
圖9 橋面鋼箱梁與鋼桁架間連接示意圖
2 加工制作的重點(diǎn)及難點(diǎn)分析
2.1 鋼桁架
2.1.1由于鋼桁架箱形梁總長(zhǎng)約215米,制作時(shí)需分段進(jìn)行加工,如何保證各分段間的接口質(zhì)量是本工程的技術(shù)重點(diǎn)。
2.1.2鋼桁架弦桿分段間以及腹桿與弦桿間均采用了栓接,其連接孔群復(fù)雜且數(shù)量較多,制作精度要求較高,增加了桿件制作的難度。
2.1.3鋼桁架腹桿與弦桿節(jié)點(diǎn)板間采用了插入式的連接方法,導(dǎo)致弦桿節(jié)點(diǎn)板間的開檔尺寸、腹桿截面尺寸的制作要求大大提高,另外,對(duì)接觸面間的平整度要求也相應(yīng)提高,是本工程加工過程中控制的重點(diǎn)。
2.1.4鋼桁架下弦兩側(cè)通過栓焊連接方式與橋面鋼箱梁及橋面人行道托架進(jìn)行連接,對(duì)下弦懸挑部分的開檔尺寸以及隔板的裝焊精度提出了更高要求。
2.2 橋面鋼箱梁
2.2.1因橋面鋼箱梁寬度達(dá)30m,頂、底板制作時(shí)需預(yù)先劃分成許多大小不等的板單元,各板單元的制作精度(板面的平整度、U形肋的開檔尺寸等)直接影響鋼箱梁的質(zhì)量,因此,板單元制作的精度是本工程控制的一大重點(diǎn)。
2.2.2由于頂板下口沿寬度方向分布了48根U形肋,U形肋中心開檔尺寸為600~900不等;底板上口沿寬度方向分布了36根U形肋,U形肋中心開檔尺寸為640~1075不等,在保證各板單元加工精度后,還需保證各板單元拼接后的整體精度(板面的整體平整度、U形肋的開檔尺寸等),這是本工程的一大難點(diǎn)。
2.2.3單塊橫隔板總寬為30m,被四塊縱向腹板分割成五塊,最小寬度為1.35m,最大寬度為12.25 m(上口分布了20個(gè)U形槽口,下口分布了15個(gè)U形槽口),橫隔板上還設(shè)置了豎向及水平方向的加勁板,橫隔板切割的精度以及裝焊后的加工精度是本工程控制的另一大難點(diǎn)。
2.2.4鋼箱梁在加工制作過程中,頂板單元的拼縫焊接導(dǎo)致箱體的變形,如何控制該變形是本工程需控制的另一大重點(diǎn)。
2.2.5橋面鋼箱梁分段與分段連接,頂、底板采用焊接,縱向腹板采用栓接,因分段寬度較大、高度較高,分段間截面尺寸的吻合以及焊縫間隙的一致性,是本工程加工制作過程中的第三大難點(diǎn);另外腹板間對(duì)接高強(qiáng)度螺栓孔的穿孔精度是本工程控制的第三個(gè)重點(diǎn)。
2.2.6橋面鋼箱梁與兩側(cè)鋼桁架箱梁連接,頂、底板也采用焊接,橫隔板間采用了栓接,與上相同,橋面鋼箱梁與兩側(cè)鋼桁架箱梁對(duì)接口的截面尺寸及焊縫間隙是本工程加工制作過程中的第四大難點(diǎn);另外橫隔板間對(duì)接高強(qiáng)度螺栓孔的穿孔精度是本工程控制的第四個(gè)重點(diǎn)。
3 加工制作的總體思路
3.1 鋼桁架部分
鋼桁架加工時(shí)首先在材料方面加以嚴(yán)格控制,確保其厚度、外形尺寸以及板面平整度。然后以各個(gè)分段為單元分別單獨(dú)進(jìn)行制作,由板單元——中合攏的加工順序,在加工制作過程中,劃線均采用鋼針進(jìn)行劃線,確保安裝位置的劃線精度;組裝時(shí)采用各種工裝確保裝配的精度;焊接時(shí)采用較小的線能量、對(duì)稱、分中的施焊方法盡可能的減小焊接變形;矯正時(shí)采用油壓機(jī)或火焰進(jìn)行矯正;鉆孔時(shí)采用數(shù)控以及鉆模套鉆的方法確保高強(qiáng)度螺栓孔的精度,層層把關(guān),精心制作,提高單件的加工精度,而后在整體預(yù)拼裝胎架上分區(qū)段進(jìn)行預(yù)拼裝。
3.2 橋面鋼箱梁部分
鋼箱梁制造時(shí),首先進(jìn)行板單元的劃分(以節(jié)段A為例),根據(jù)截面形式同時(shí)結(jié)合材料板寬限制等因素,將頂板劃分為12個(gè)板單元,寬度為2400~2750mm不等;將頂板劃分為13個(gè)板單元,寬度為1850~2550mm不等。縱向腹板各自為一個(gè)板單元,共計(jì)4個(gè);每檔橫隔板被縱向腹板分割成五塊,每塊為一個(gè)板單元,見圖10所示。
為了便于制作,各板單元均應(yīng)分別進(jìn)行編號(hào),其編號(hào)原則為:所有節(jié)段板單元均以該節(jié)段字母開頭,底板單元以橋面中心線為準(zhǔn),中心線處單元板后綴為A0,從中向左依次為A1~A6、從中向右依次為B1~B6;頂板單元以橋面中心線為準(zhǔn),從中向左依次為C1~C6、從中向右依次為D1~D6;所有節(jié)段頂、底板單元?jiǎng)澐治恢镁嗤唧w位置見圖11所示。
各節(jié)段板單元?jiǎng)澐趾螅謩e預(yù)先進(jìn)行各節(jié)段板單元(頂、底板單元、縱向腹板單元、橫隔板單元)的小合攏裝焊,合格后分區(qū)段在整體組裝胎架上采用正造法輪次進(jìn)行中合攏裝焊。而后各節(jié)段分別與相對(duì)應(yīng)鋼桁架箱形梁進(jìn)行預(yù)拼。
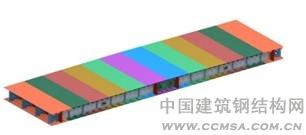
圖10
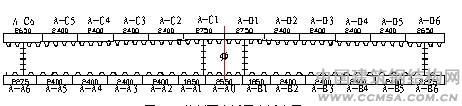
圖11 此剖面為橋尾向橋中看
4 加工制作的關(guān)鍵技術(shù)及保證措施
4.1 材料
鋼桁架所用鋼材材質(zhì)均為Q345QD,必須符合設(shè)計(jì)文件的要求和現(xiàn)行標(biāo)準(zhǔn)的規(guī)定,除有材料質(zhì)量證明書外,還應(yīng)進(jìn)行復(fù)驗(yàn),復(fù)驗(yàn)合格后方能使用。因本工程結(jié)構(gòu)的特殊性,鋼桁架箱梁的板厚必須嚴(yán)格控制,以免加工過程中出現(xiàn)板邊差影向構(gòu)件的加工質(zhì)量以及高強(qiáng)度螺栓的連接質(zhì)量。
4.1.1 鋼材的矯平
由于本工程加工制作精度要求高,任何的積累誤差都會(huì)影響到質(zhì)量控制,為此鋼板進(jìn)廠后先采用鋼板矯平機(jī)對(duì)鋼板進(jìn)行矯平,達(dá)到每平米平整度不大于1mm,矯平的目的是消除鋼板的殘余變形和減少軋制內(nèi)應(yīng)力,從而可以減少制造過程中的變形,見圖12所示:
圖12七輥矯平機(jī)零件二次矯平
4.1.2 鋼材的預(yù)處理
采用專用鋼板預(yù)處理生產(chǎn)線對(duì)鋼板進(jìn)行除銹,噴車間底漆和烘干,保證鋼材的除銹質(zhì)量達(dá)到Sa2.5級(jí),見圖13所示:所有鋼板均進(jìn)行預(yù)處理,其過程為:矯平→拋丸、除銹→噴漆→烘干
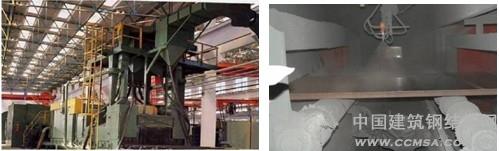
圖13鋼板預(yù)處理
4.2 下料、切割、刨邊
構(gòu)件放樣采用計(jì)算機(jī)放樣技術(shù),放樣時(shí)必須將工藝需要的各種補(bǔ)償余量加入整體尺寸中,為了保證切割質(zhì)量,厚板切割前先進(jìn)行表面滲碳硬度試驗(yàn)。
本公司吸收國(guó)外先進(jìn)工藝,切割優(yōu)先采用數(shù)控精密切割設(shè)備進(jìn)行設(shè)割,選用高純度98.0%以上的丙稀氣加99.99%的液氧氣體,可保證切割端面光滑、平直、無缺口、掛渣,坡口采用專用進(jìn)口切割機(jī)進(jìn)行切割,見14圖所示。
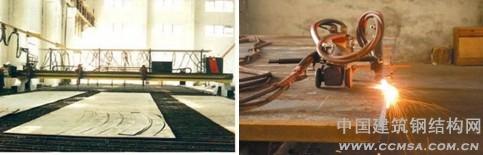
圖14數(shù)控切割機(jī)數(shù)控直條切割機(jī)等離子數(shù)控切割機(jī)坡口專用切割機(jī)
箱形構(gòu)件的上、下蓋板及橫隔板、H形構(gòu)件的腹板及有磨光頂緊要求的接觸面等均采用刨邊機(jī)(見圖15)或銑邊機(jī)加工。
H形構(gòu)件的腹板、箱形構(gòu)件的上、下蓋板的加工寬度尺寸確定,除考慮焊接收縮量等因素外,還應(yīng)考慮與其組裝的翼板或腹板的板厚偏差,以確保構(gòu)件的截面尺寸精度。
邊緣的刨銑加工深度不應(yīng)小于3mm(當(dāng)邊緣硬度不超過HV350時(shí),其加工可不受此限制),加工 面粗糙度不高于25μm,頂緊傳力面加工粗糙度不應(yīng)高于12.5μm,頂緊加工面與板面的垂直度偏差,應(yīng)小于板厚的1%,且不得大于0.3 mm。
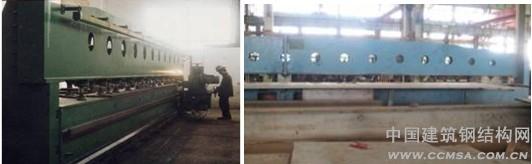
圖15機(jī)加工銑邊
4.3 鋼桁架加工難點(diǎn)及重點(diǎn)的控制措施
4.3.1 桿件幾何尺寸精度的保證
為保證桿件拼裝時(shí)拼接板與桿件間的間隙符合規(guī)范要求,保證桿件端口尺寸的一致性,制作時(shí)同一接口采用同批次同厚度材料下料,端口采用機(jī)加工工裝隔板進(jìn)行控制,大大減小了對(duì)接口的板厚錯(cuò)變量,見16圖所示。
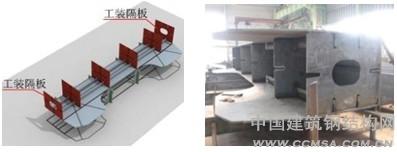
圖16箱梁組裝
4.3.2 桿件焊接變形的控制
桿件板單元焊接變形的控制是桿件制造的基本要求,也是桿件制造的關(guān)鍵點(diǎn),板單元小合攏焊接完成后有規(guī)律的輕微焊接變形可通過機(jī)械矯正措施解決,因此,桿件焊接變形的控制是鋼桁梁桿件制造的重點(diǎn)也是關(guān)鍵點(diǎn),見17圖所示。
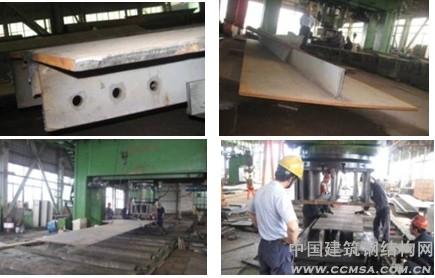
圖17板單元的校正
4.4.3 鋼桁架箱梁分段間栓接精度的控制
這種特殊的全栓接鋼桁梁的制造鉆孔精度是保證結(jié)構(gòu)整體受力及整體成橋線型精度的關(guān)鍵所在。首先將鋼桁架箱梁無節(jié)點(diǎn)板一端采用高精度數(shù)控機(jī)床制作專用鉆模(螺栓孔徑及孔距偏差控制在5絲之內(nèi))進(jìn)行套鉆鉆孔(分段間連接板與之相同)。
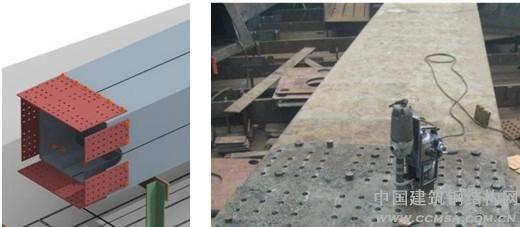
圖18上弦桿端口的預(yù)先鉆孔圖
而后將鋼桁架分段采用分輪次循環(huán)預(yù)拼裝的方法,將分段間的連接板采用工裝銷軸螺栓進(jìn)行固定,合格后采用磁座鉆進(jìn)行鋼桁架分段節(jié)點(diǎn)板端螺栓孔的全位置一次性配鉆出孔。
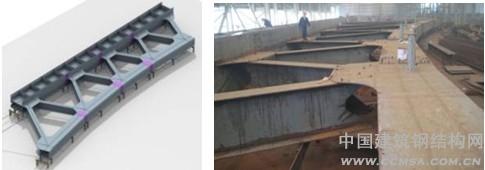
圖19 箱梁的循環(huán)拼裝
圖20相鄰分段端口的鉆孔
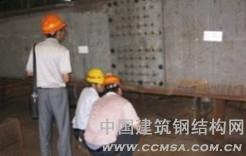
圖21 螺栓孔的驗(yàn)收
4.5 鋼箱梁加工難點(diǎn)及重點(diǎn)的控制措施
4.5.1 板單元精度控制
板單元制作時(shí),整體鋪板,采用鋼帶統(tǒng)一劃線、安裝U形肋(U型肋內(nèi)部應(yīng)預(yù)先進(jìn)行涂裝),同時(shí)采用樣板檢測(cè),合格后各板單元分別在專用反變形焊接胎架上進(jìn)行施焊,確保其精度。
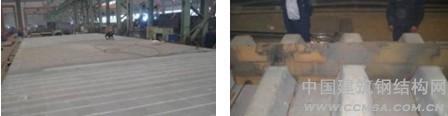
圖22 板單元的組裝
圖23 板單元的焊接
4.5.2 底板的整體平整度及U肋開檔尺寸控制
為了有效的控制底板板單元間U形肋的開檔尺寸,中合攏前可將相鄰兩塊板單元預(yù)先拼接(預(yù)放 一定的焊接收縮量以及角變形,待焊了幾塊后也可掌握拼板間實(shí)際的焊接收縮及角變形量),而后再進(jìn)行拼裝(各板單元間縱縫按實(shí)際焊接收縮量進(jìn)行加放),適當(dāng)矯正,從而控制住底板U形肋的開檔尺寸以及板面的平整度。
4.5.3 橫隔板單元精度的控制
橫隔板下料時(shí)采用數(shù)控等離子切割,切割后采用專用樣板進(jìn)行檢查,加勁板與橫隔板焊接時(shí)采用 CO2氣保焊配以小電流、小電壓的焊接方法進(jìn)行施焊,有效減少焊接變形,控制橫隔板單元的質(zhì)量。
4.5.4 橋面鋼箱梁角變形的控制
頂板單元縱縫焊接會(huì)造成一定的焊接角變形,此焊接角變形的解決方法是:在確保胎架制作精度的基礎(chǔ)上,另外在胎架上另外增設(shè)墊板,制作出一反變形,以抵消頂板焊接所造成的變形。
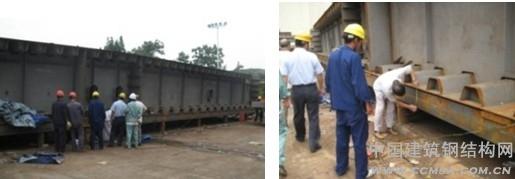
圖24 角變形的檢查
4.5.5 橋面鋼箱梁分段間的接口保證措施
(1)橋面鋼箱梁制造時(shí),采用幾個(gè)分段一起整體拼裝,組裝及焊接均采用相同的方法進(jìn)行,另外在分段接口處預(yù)留一段不焊,待分段組對(duì)合格后進(jìn)行施焊,確保分段間對(duì)接的平齊。
(2)兩分段接口處一端正作,另一端加放余量進(jìn)行配切,確保接口焊縫間隙。
(3)分段間縱向腹板的螺栓孔,正作端預(yù)先鉆孔,另一端可在相鄰分段制作合格后采用現(xiàn)場(chǎng)連接板進(jìn)行配鉆,確保腹板栓接的質(zhì)量。
4.5.6 橋面鋼箱梁與鋼桁架箱梁間接口保證措施
(1)橋面鋼箱梁在裝焊過程中,兩側(cè)開口處適當(dāng)加設(shè)臨時(shí)支撐予以加強(qiáng),確保與鋼桁架箱梁間連接的開檔尺寸。
(2)橋面鋼箱梁兩側(cè)預(yù)留配切余量,待箱體焊接、矯正合格后再進(jìn)行切割,確保與鋼桁架箱梁間接口的焊縫間隙。
(3)橋面鋼箱梁與鋼桁架箱梁相連接的橫隔板,安裝時(shí)先進(jìn)行初定位,待預(yù)拼時(shí)再精確定位,而后施焊,同時(shí)采用現(xiàn)場(chǎng)連接板將其螺栓孔進(jìn)行套鉆(鋼桁架連接板已經(jīng)制孔,現(xiàn)場(chǎng)連接板也預(yù)先制孔,橋面鋼箱梁邊側(cè)連接板后鉆),以保證橫隔板連接的精度。
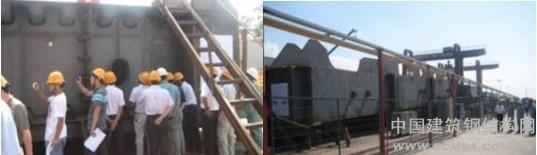
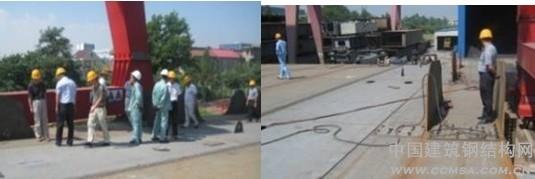
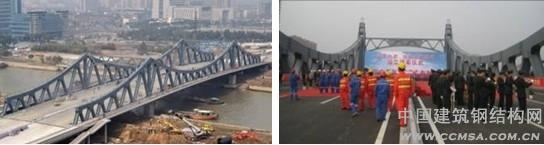
5、結(jié) 語(yǔ)
通過無錫匱大橋鋼結(jié)構(gòu)工程的制造實(shí)踐,在總結(jié)了以往大型公路、鐵路橋梁鋼構(gòu)件制作經(jīng)驗(yàn)的基礎(chǔ)上,制定了一套適合本工程鋼桁架、鋼箱梁結(jié)構(gòu)特點(diǎn)、施工條件的工藝技術(shù)方案和質(zhì)量保證措施,鋼桁架、鋼箱梁的焊接質(zhì)量、幾何尺寸精度、穿孔率等均滿足了設(shè)計(jì)要求,此種下承式鋼桁架+鋼箱梁結(jié)構(gòu)體系的制作工藝技術(shù)為今后類似橋梁的設(shè)計(jì)和制造提供了新的思路和經(jīng)驗(yàn)參考。
參考文獻(xiàn)
[1] JTJ 041-2000 公路橋涵施工技術(shù)規(guī)范[S]
[2] TB 10212-2009 鐵路鋼橋制造規(guī)范[S]
作者簡(jiǎn)介:李翠光(1965-)江蘇滬寧鋼機(jī)股份有限公司,高級(jí)工程師,
聯(lián)系地址:江蘇省宜興市張渚鎮(zhèn)百家村(214231)。
"歡迎大家轉(zhuǎn)摘!轉(zhuǎn)載須注明中國(guó)建筑金屬結(jié)構(gòu)協(xié)會(huì)建筑
鋼結(jié)構(gòu)網(wǎng)(www.fsled.com.cn)謝謝合作!"